De belangrijkste onderdelen van de A350 XWB, zoals de romp, vleugels, motoren en staartvlakken, worden geproduceerd in de Europese productiefaciliteiten van Airbus in Frankrijk, Duitsland, Spanje en het VK. De A350 XWB Final Assembly Line (FAL) in Toulouse zet vervolgens alle vliegtuigonderdelen in elkaar als een hightech puzzel.
De romp van de A350 XWB bestaat uit drie hoofdonderdelen - de voorsectie, de middensectie en een staartsectie. Alle secties - inclusief het landingsgestel - worden geassembleerd op het eerste hoofdassemblagestation, de P50. Zodra deze stap is voltooid, wordt de romp naar het P40 assemblagestation getransporteerd, waar de vleugel- en staartsectie worden samengevoegd. De eindmontagelijn is uiterst flexibel. Hij kan gebruikt worden voor zowel de A350-900 als de -1000 modellen.
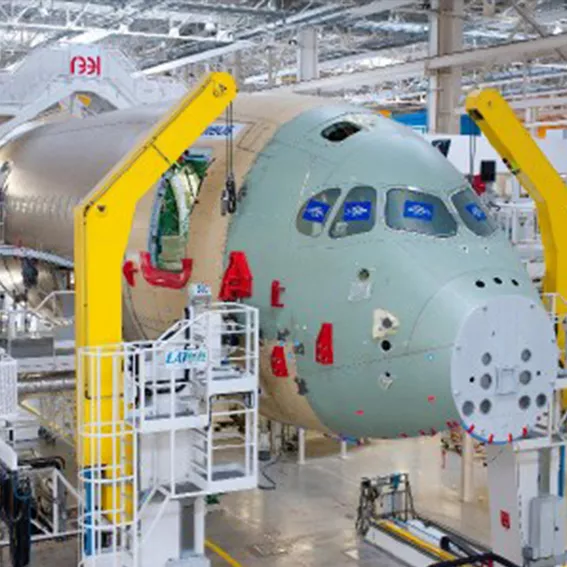
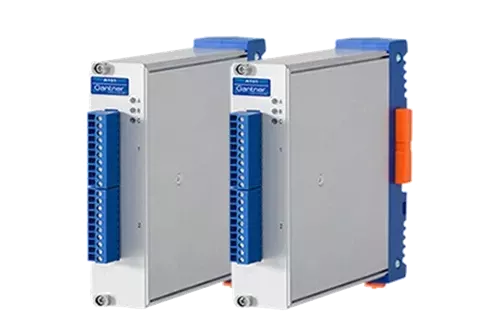
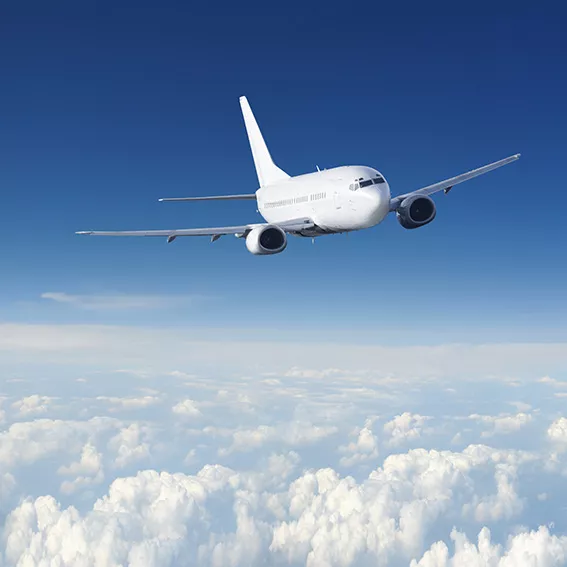
Montage
Het samenvoegen en verbinden van de grote assemblages is een complexe taak. Vooral bij onderdelen van koolstofvezelversterkte kunststof (CFRP), die in grote hoeveelheden worden gebruikt op de A350 XWB, leiden zwaartekracht en omgevingsomstandigheden tot geometrische vervormingen. Om een betrouwbare lokalisatie en positionering van de grote vliegtuigonderdelen te garanderen, wordt een op metrologie gebaseerd assemblagesysteem gebruikt. Een reeks meerassige positioneersystemen tilt, beweegt en lijnt de romp- en vleugelstructuur uit om de beste pasvorm te garanderen. Om de grote onderdelen tijdens het uitlijnen zo goed mogelijk te beschermen, worden er loadcellen gebruikt die in het aandrijfmechanisme van de positioneerder zijn gemonteerd. Ze worden gebruikt om de krachten te meten die tijdens de beweging op de structuur inwerken. Mogelijke schade door spanningen op de onderdelen tijdens de assemblage wordt zo voorkomen.
Het hele assemblagesysteem bevat 300 loadcellen. Eenassige loadcellen bewaken de slag (Fz) en triaxiale loadcellen bewaken de kracht tijdens assemblage (Fx, Fy en Fz). Alle loadcellen hebben een dubbele bruguitgang voor redundantie in het systeem. De loadcellen zijn aangesloten op een Gantner Q.bloxx meetsysteem. In totaal worden 150 Q.bloxx A101 modules gebruikt voor primaire krachtbewaking. Daarnaast worden 300 Q.bloxx A102 modules gebruikt voor redundante bewaking.
Functionaliteit van het meetsysteem
De afstand tussen de meetcel en het monitoringsysteem kan oplopen tot 75 meter. Het plaatsen van de signaalomzetters dicht bij de eigenlijke meetpunten is een van de belangrijkste eisen bij het ontwerpen van een assemblagesysteem op basis van metingen. De optimale kanaalgranulariteit van de Q.bloxx, gecombineerd met de mogelijkheid om modules vrij te combineren en te verdelen, biedt Airbus maximale flexibiliteit. De modules communiceren via RS-485 met een centraal geplaatste Q.station controller, die de taken van gegevensverzameling, synchronisatie en besturing overneemt. De gegevens worden verzonden via een zeer efficiënt protocol met een baudrate tot 48 MBaud. Ondanks het decentrale ontwerp is de meting synchroon met een jitter van minder dan 1 µs. Deze architectuur zorgt voor betrouwbare meetresultaten met slechts minimale bekabeling.
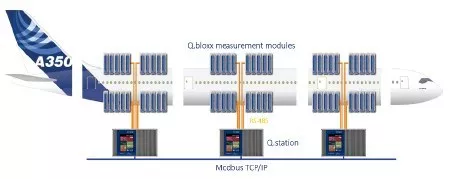
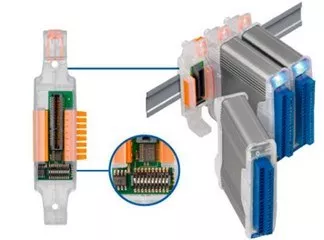
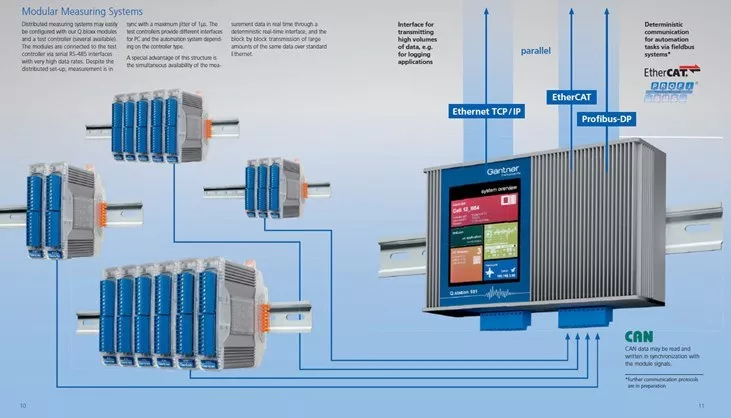
Functie en structuur van de meetoplossing
De Q.bloxx A101 en A102 hebben ingebouwde microprocessors, 24-bits A/D converters, anti-alias hardwarefilters en volledige 3-weg isolatie tot 500 VDC op elk kanaal. De meetmodules ondersteunen bemonsteringsfrequenties tot 100 kHz per kanaal.
Omdat de overdracht van grote hoeveelheden ruwe gegevens een zware belasting vormt voor de netwerkbronnen, is elke module uitgerust met een FPGA. Dit maakt volledige signaalconditionering en gegevensverwerking mogelijk direct op het punt waar de sensorgegevens het meetsysteem binnenkomen. Zo worden alleen gegevens met procesrelevante informatie, zoals gemiddelde waarde, min/max en piekpiekmeting, naar het monitoringsysteem gestuurd. Dit voorkomt lange laadtijden en verbetert de responstijden.
Q.bloxx voor decentrale, snelle en nauwkeurige metingen
De kosten voor de montage van het passagierscompartiment bedragen tot 40% van het totale bouwbudget. Daarom is de betrouwbare beschikbaarheid van het montagesysteem hier bijzonder belangrijk. Elke Q.bloxx module is verbonden met een socket die een ingebouwde flashgeheugenchip bevat met een kopie van de volledige moduleconfiguratie. Dit betekent dat wanneer een defecte module wordt vervangen, het niet nodig is om de nieuwe module of het monitoringsysteem handmatig opnieuw te configureren. De modules kunnen tijdens bedrijf worden vervangen zonder dat de voeding moet worden uitgeschakeld. In slechts 5 seconden wordt de configuratie van het stopcontact naar de nieuwe module gekopieerd. De meting wordt automatisch voortgezet zodra de configuratie is hersteld. De Q.bloxx "hot swap" functie maakt efficiënt onderhoud en service van het meetsysteem mogelijk, minimaliseert de uitvaltijd en verhoogt de efficiëntie van de eindmontagelijn.
Grafiek 1: @AIRBUS S.A.S. 2012 foto door e*m company / P. Pigeyre
overige foto's/grafieken: GI