Die wichtigsten Teile des A350 XWB wie Rumpf, Tragflächen, Triebwerke und Leitwerk werden in den europäischen Produktionsstätten von Airbus in Frankreich, Deutschland, Spanien und Großbritannien gefertigt. In der A350 XWB-Endmontagelinie (FAL) in Toulouse werden dann alle Flugzeugteile wie ein Hightech-Puzzle zusammengesetzt.
Der Rumpf des A350 XWB besteht aus drei Hauptteilen – Vorder- und Mittelteil sowie einem Heckbereich. Alle Bereiche – inklusive des Fahrwerks- werden an der ersten Hauptmontagestation, der P50, zusammengefügt. Ist dieser Schritt abgeschlossen, wird der Rumpf zur Montagestelle P40 transportiert, wo die Flügel- und der Heckbereich zusammengefügt werden. Die Endmontagelinie ist extrem flexible. Sie kann sowohl für den A350-900- als auch für die -1000-Modelle eingesetzt werden.
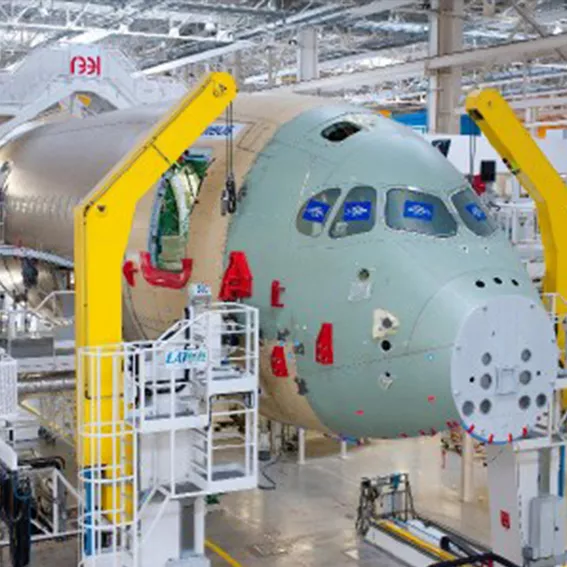
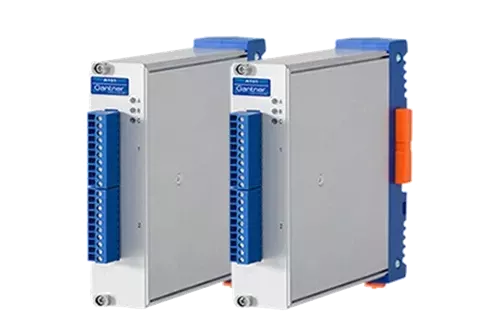
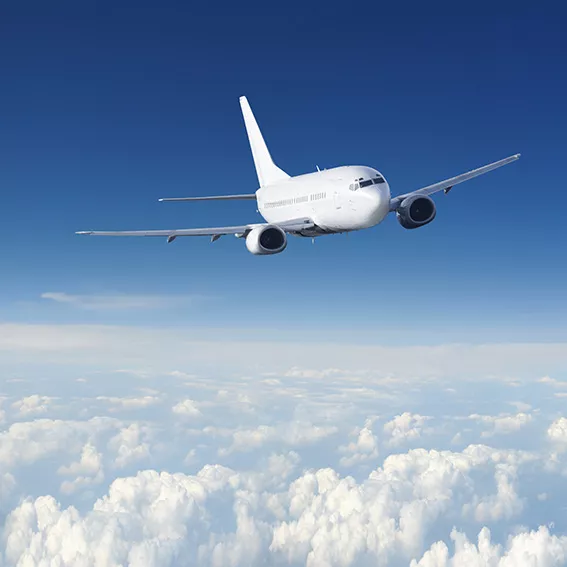
Prozess des Zusammenfügens
Der Prozess des Zusammenfügens und Verbindens der großen Baugruppen ist eine komplexe Aufgabe. Gerade bei Bauteilen aus kohlenstofffaserverstärktem Kunststoff (CFK), die beim A350 XWB in großen Mengen eingesetzt werden, führen Schwerkraft und Umgebungsbedingungen zu geometrischen Verformungen. Um eine sichere Lokalisierung und Positionierung der großen Flugzeugteile zu gewährleisten, wird ein das Montagesystem messtechnisch unterstützt. Eine Reihe von mehrachsigen Positionierungssystemen hebt, bewegt und richtet die Rumpf- und Tragflächenstruktur aus, um die optimale Passgenauigkeit sicher zu stellen. Um die großen Teile während der Ausrichtung bestmöglich zu schützen, kommen Wiegezellen zum Einsatz, die im Antriebsmechanismus des Positionierers montiert sind. Mit ihrer Hilfe werden die auf die Struktur wirkenden Kräfte während der Bewegung überwacht. Mögliche Beschädigungen durch Spannungen und Belastungen der Teile während des Zusammenfügens werden so vermieden.
Das gesamte Montagesystem enthält 300 Wägezellen. Einachsige Wägezellen überwachen den Hub (Fz) und dreiachsige Wägezellen überwachen die Kraft während der Montage (Fx, Fy und Fz). Alle Wägezellen haben einen Dual-Bridge-Ausgang, um eine Redundanz im System zu ermöglichen. Die Wägezellen sind an ein Gantner Q.bloxx Messsystem angeschlossen. Insgesamt 150 Q.bloxx A101 Module werden für die primäre Kraftüberwachung eingesetzt. Zusätzlich werden 300 Q.bloxx A102 Module für die redundante Überwachung eingesetzt.
Der Abstand zwischen Wägezelle und Monitoringsystem kann bis zu 75 Meter betragen. Die Platzierung der Signalwandler in der Nähe der eigentlichen Messpunkte ist eine der wichtigsten Anforderungen bei der Konzeption eines messgestützten Montagesystems. Die optimale Channel-Granularität des Q.bloxx, kombiniert mit der Möglichkeit, Module frei zu kombinieren und zu verteilen, bietet Airbus maximale Flexibilität. Die Module kommunizieren über RS-485 mit einem zentral positionierten Q.station-Controller, der die Aufgaben der Datenerfassung, Synchronisation und Steuerung übernimmt. Die Datenübertragung erfolgt über ein sehr effizientes Protokoll mit einer Baudrate von bis zu 48 MBaud. Trotz desdezentralen Aufbaus erfolgt die Messung synchron mit einem Jitter von weniger als 1 µs. Diese Architektur gewährleistet zuverlässige Messergebnisse bei nur geringem Verkabelungsaufwand.
Das Überwachungssystem für das Fließband beinhaltet eine Schneider Electric Safety PLC. Der Q.station Controller in offener Architektur kommuniziert mit der Safety PLC über Modus TCP/IP. Durch die Trennung des Q.station Controllers von den Messmodulen wird die Kommunikation und Kompatibilität mit dem Überwachungssystem deutlich optimiert. Ein weiterer Vorteil ist für Airbus die Möglichkeit eines Controller-Tauschs, wenn sich die Schnittstellen- oder Leistungsanforderungen ändern– ohne größere Neuinvestitionen.
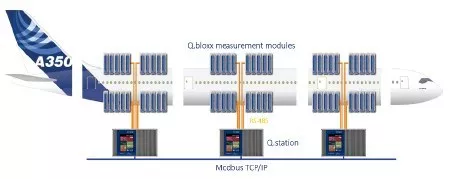
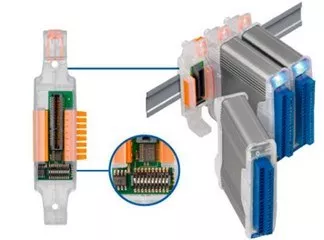
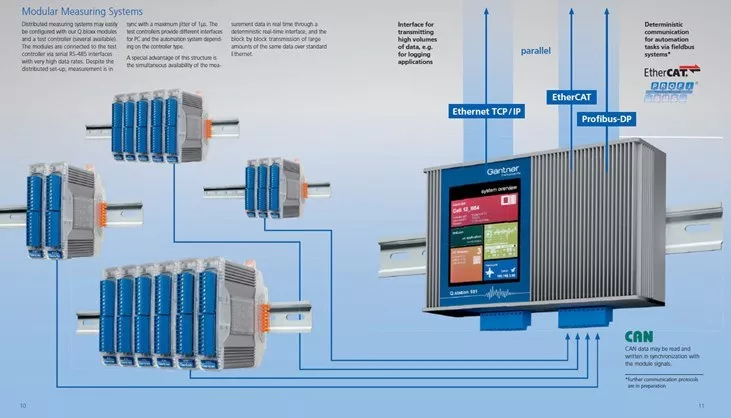
Funktion und Aufbau der Messlösung
Die Q.bloxx A101 und A102 verfügen über On-Board-Mikroprozessoren, 24-Bit-A/D-Wandler, Anti-Alias-Hardwarefilter und eine vollständige 3-Wege-Isolation bis 500 VDC auf jedem Kanal. Die Messmodule unterstützen Abtastraten von bis zu 100 kHz pro Kanal.
Da die Übertragung großer Mengen an Rohdaten die Netzwerkressourcen stark belastet, ist jedes Modul mit einem FPGA ausgestattet. Dieser ermöglicht eine vollständige Signalkonditionierung und Datenverarbeitung direct an der Stelle, and der die Sensordaten in das Messsystem gelangen. So werden nur Daten mit prozessrelevanten Informationen, wie Mittelwert, Min/Max und Peak-Spike-Messung an das Überwachungssystem gesendet. Dies vermeidet lange Ladezeiten und verbessert die Reaktionszeiten.
Q.bloxx für dezentrales, schnelles und genaues Messen
Die Kosten für die Montag der Fluggastzelle belaufen sich sich auf bis zu 40% des gesamten Budgets für den Bau. Daher ist gerade hier die zuverlässige Verfügbarkeit des Montagesystems von besonders hoher Bedeutung. Jedes Q.bloxx-Modul wird mit einem Sockel verbunden, der einen eingebauten Flash-Speicherchip mit eine Kopie der gesamten Modulkonfiguration enthält. Damit ist bei einem Austausch eines defekten Moduls keine manuelle Neukonfiguration des neuen Moduls oder des Überwachungssystems notwendig. Die Module können im laufenden Betrieb ausgetauscht werden, ohne dass die Stromversorgung abgeschaltet werden muss. In nur 5 Sekunden wird die Konfiguration vom Sockel auf das neue Modul kopiert. Die Messung wird automatisch fortgesetzt, sobald die Konfiguration wiederhergestellt ist. Die Q.bloxx "Hot Swap"-Funktion ermöglicht eine effiziente Wartung und Instandhaltung des Messsystems, minimiert die Ausfallzeiten und erhöht die Effizienz der Endmontagelinie.
Grafik 1: @AIRBUS S.A.S. 2012 photo by e*m company / P. Pigeyre
restliche Fotos/Grafiken: GI