Fast torque sensors measure the motors
Previously, Project MARCH used position-controlled motors. However, a balanced exoskeleton requires a compliant system: this means that the motors must be able to yield and/or give back pressure in response to their environment. Therefore, Project MARCH wanted to use torque sensors for the first time. These sensors had to be able to measure the total range of the motors, and most importantly have a high update frequency. The faster the sensors are, the faster it is possible to react to imbalance. The sensors also had to fit into the existing motors and joints. Together with Althen, these sensors were designed, for both the linear and rotational motor. These motors simulate the muscle movement of the human body, which is they are called joints.
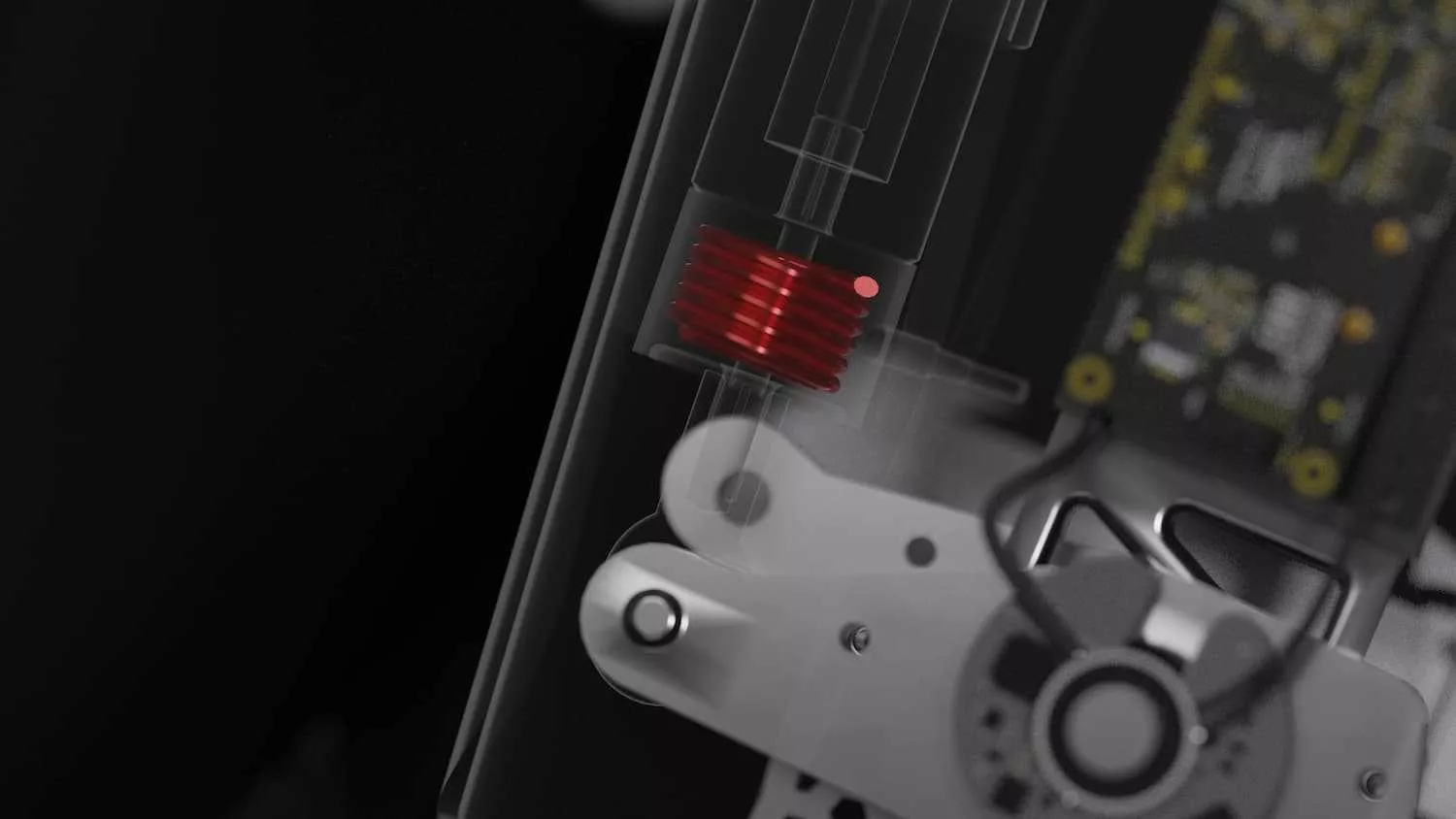
Requirements of the sensors
The design process of the sensors had two major obstacles: the sensors had to have a high update rate and fit within existing hardware and software architecture. A certain level of accuracy was of course also required, although it was especially important to measure substantial differences per motor. In the end, Althen helped to make sensors that fitted on an already existing part of our exoskeleton, inside the motor housing. For the linear joints, it was possible to place an existing sensor on the spindle of the motor. Both sensors could be linked to the rest of the system with a new embedded communication protocol.
Spindle of the linear joints and motor force
Althen supplied two type of sensors: load cells and torque transducers. The load cells were installed on the spindle of the linear joints. The sensors are quick to install, plug and play so to speak. The other sensors, the torque transducers, are installed in the metal part that transfers the force from the motor to the leg. To start testing, these sensors must be placed inside the motor assemblies. Project March then tests the sensors separately in a test setup: communication protocols, speeds and adjustment of the sensors take place here. Based on the sensors, the motos are controlled, so the control loop is also tested here.
The predictive algorithm required a lot of sensor data, especially information about the forces on different joints. With that question, Project March came to Althen
Testing the sensors
The predictive software that can outline different future scenarios through sensor input; all scenarios are given a score of how balanced they are, and the most balanced scenario (i.e., with the highest score) is executed. Project March is still in the early stages of testing the sensors after waiting for delivery, so for now not all the results are available yet. Currently, Project March has communication with the sensors via the newly integrated protocol. At this moment the tests in the aforementioned test setup will start.
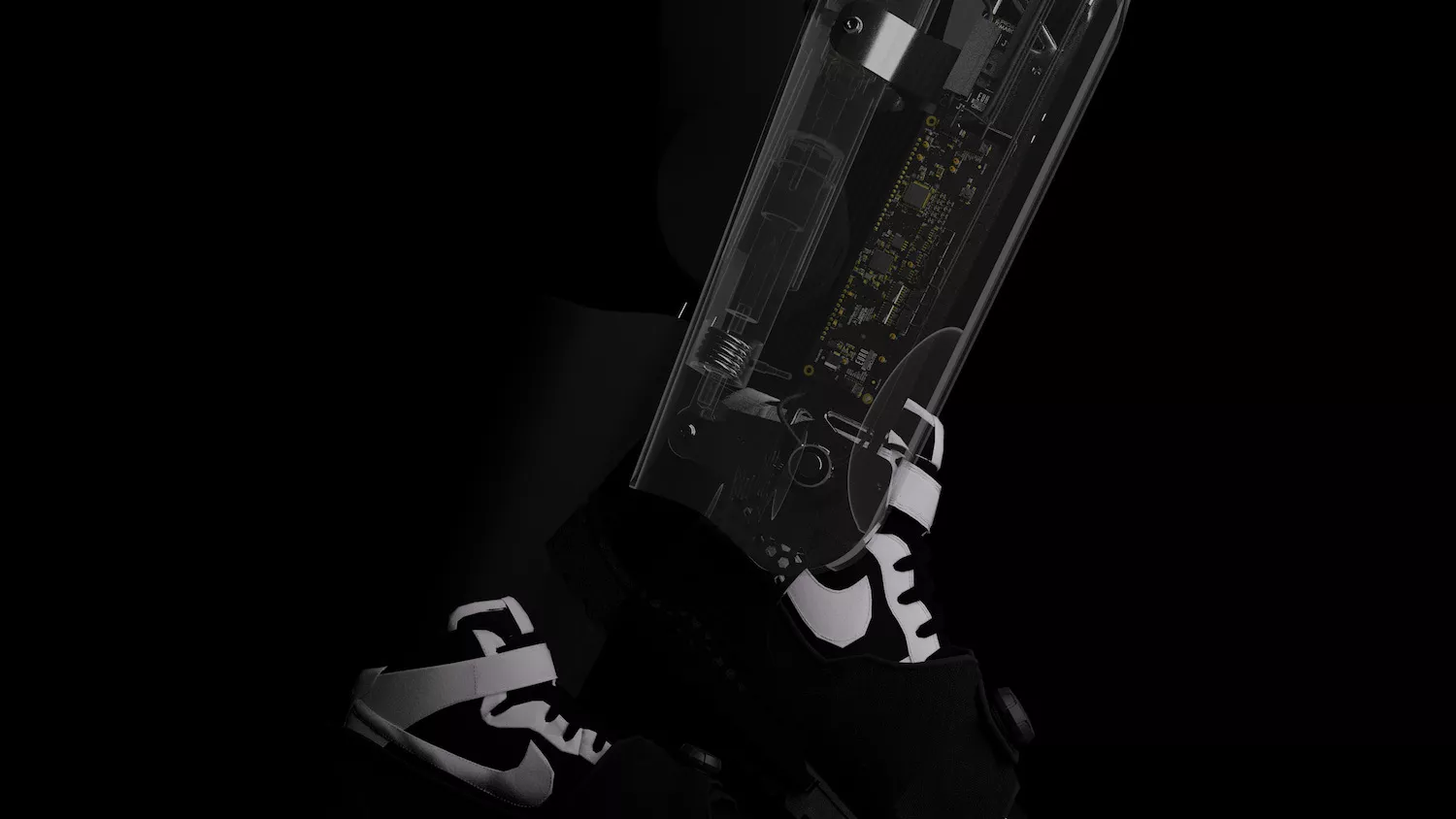
Placing the sensors in the exoskeleton
Then it is time to place the sensors in the exoskeleton. Once a motor (including sensors) is fully tested in the test setup, it can be placed in the exoskeleton. But before the user can enter the exoskeleton, more tests need to be done. First, the exo is allowed to move freely in the air, a so-called airgait. During the airgait, the exoskeleton (eventually torque controlled with new sensors) moves in a gait pattern. If this goes well, the exoskeleton can perform a “groundgait”. Here, the exoskeleton again walks in the aforementioned gait pattern, but on the ground. Once all this is done, the user (or pilot as we call it), can enter the exoskeleton.
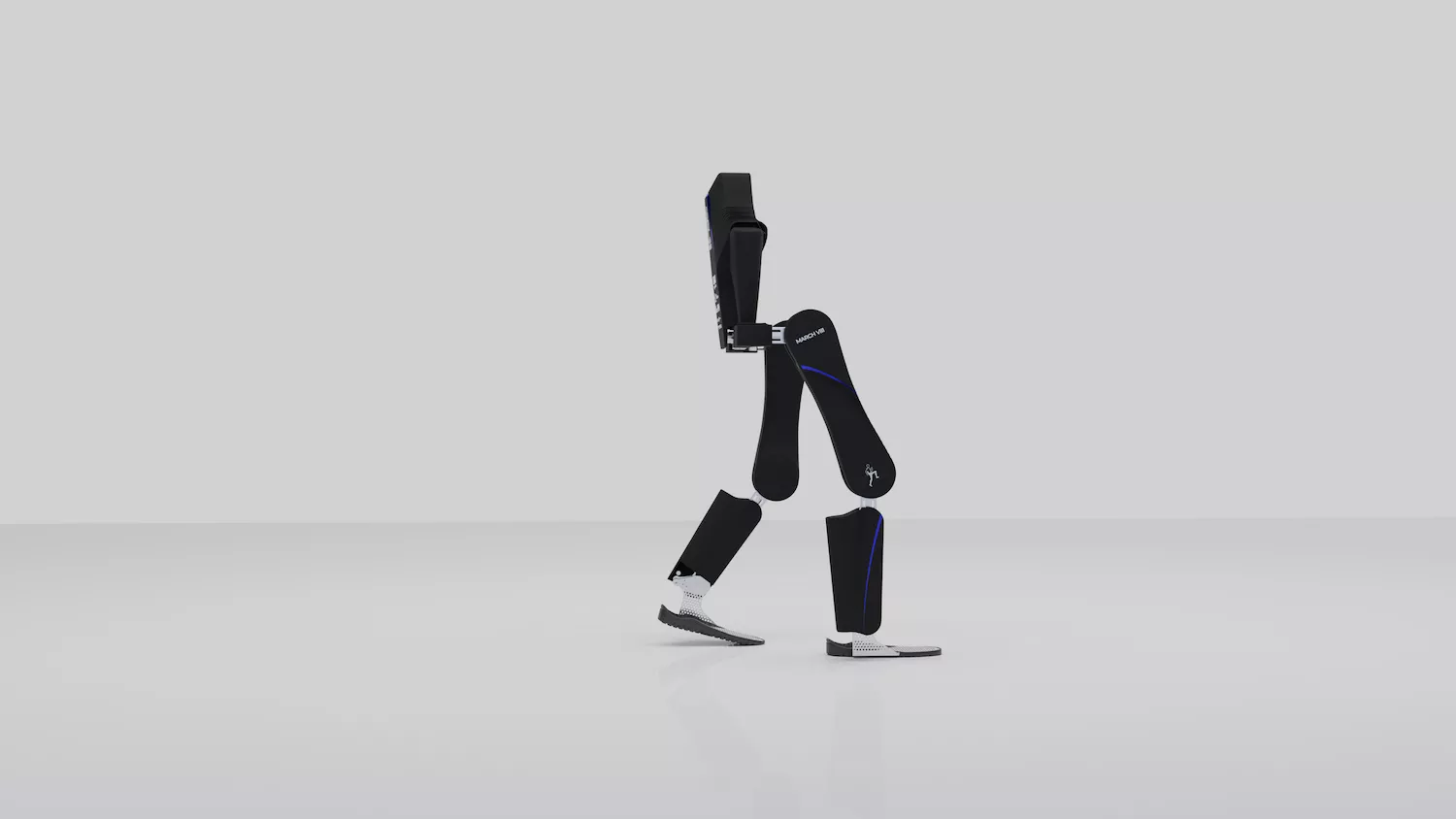
The exoskeleton responds
By using Althen's torque sensors, it is possible to build a compliant system that can measure external influences through sensors for the first time. In other words, through these sensors, the exoskeleton can respond to input and imbalance from the outside world, making the MARCH 8 one of the first self-balancing exoskeletons in the world. Project March will show this to the world in the Exoskelet Reveal on the 21st of July! Would you like to know more about Project March, torque sensors, or load cells? Please let us know what your measurement challenge is.