BM-Heavy Feeder platform stabilizes the GE Haliade X
In 2023, Althen Sensors & Controls delivered four heavy duty load pins to Barge Master for their new Heavy Feeder Platform. This “BM-Heavy Feeder” is a motion-compensated platform which provides a feeder solution for the next generation of wind turbines, which are increasingly getting larger and larger. In the Vineyard Wind Project, a new development off the east coast of the United States, the BM-Heavy Feeder platform has been working to stabilize the GE Haliade X tower sections, which can weigh over 700 metric tons a piece.
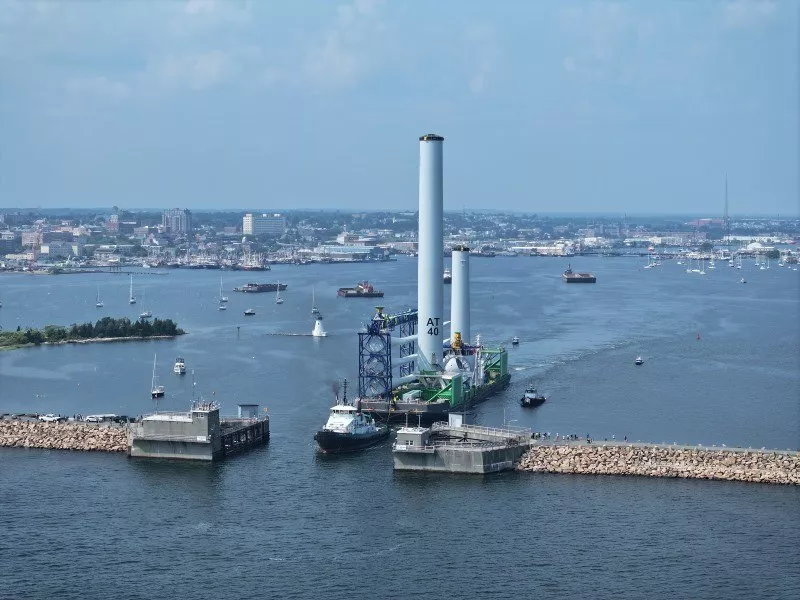
Securely fastened during transit
The BM-Heavy Feeder platform is installed on barges, which are towed from a harbor to the wind turbine installation vessel, which is usually a jack-up barge. During transit, the Heavy Feeder platform is “locked” and inactive, thus not compensating the motion of the waves underneath. Therefore, the platform must be able to withstand the dynamic impact loads of the full weight of the tower sections caused by waves during transit. The Transit Docking System (“TDS”) makes sure that the tower sections are securely fastened during transit and that the BM-Heavy Feeder can withstand all dynamic loads.
Rated for 1.680 tonnes each
When the barge arrives at the wind turbine installation vessel, the weight of the towers is compensated with large pistons, so that the stabilization platform can “take over” and compensate the motion of the waves with regards to the installation vessel. The custom Althen ALP load pins, rated for 1.680 tonnes each, provide a force measurement to make sure that all weight of the tower sections is compensated and that the platform is at “net zero weight” before the active stabilization system takes over.
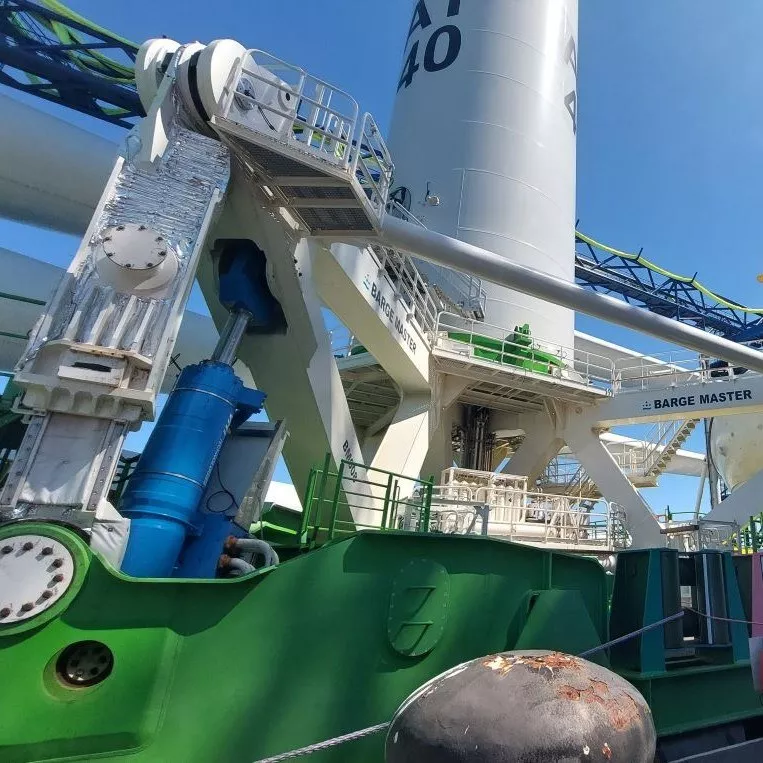
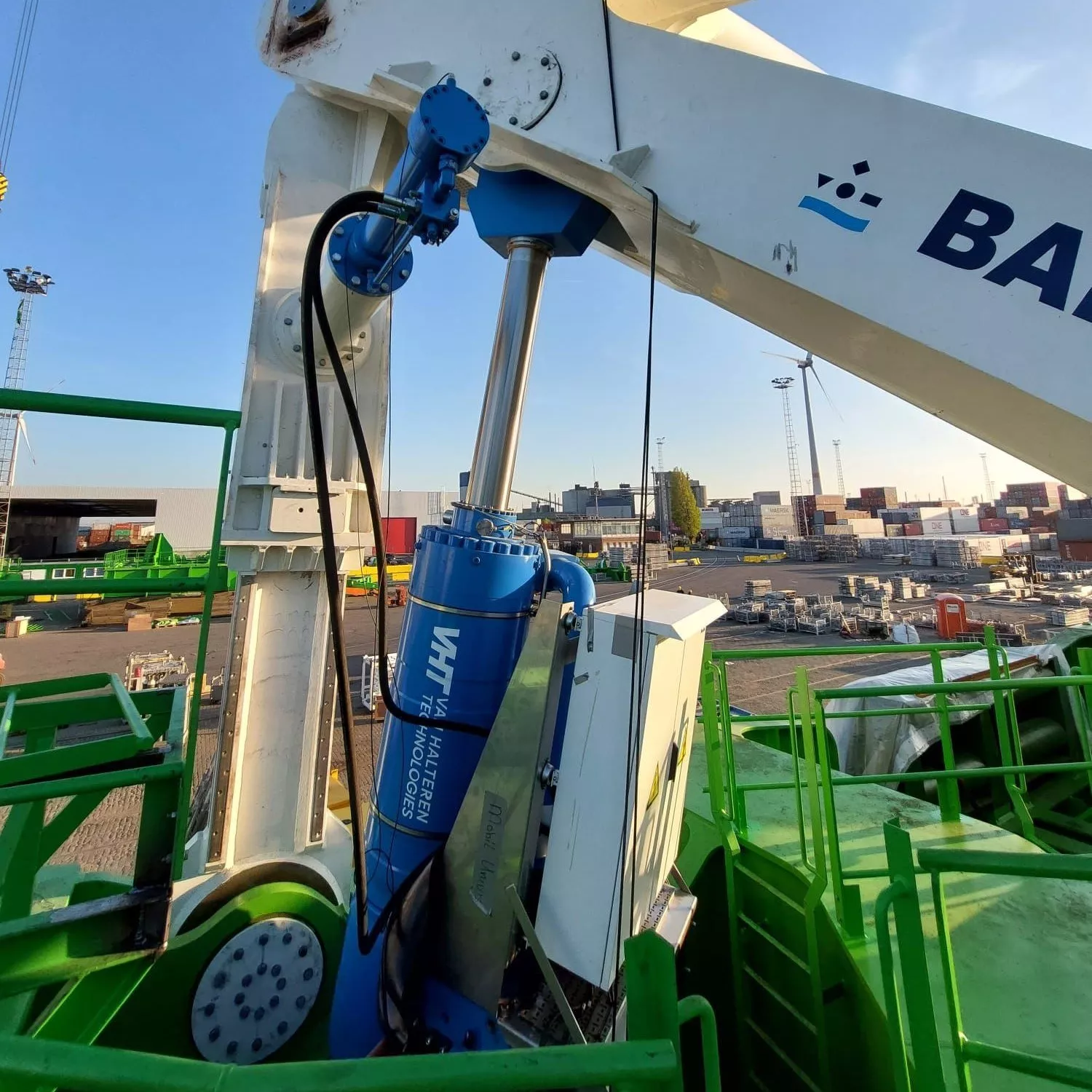
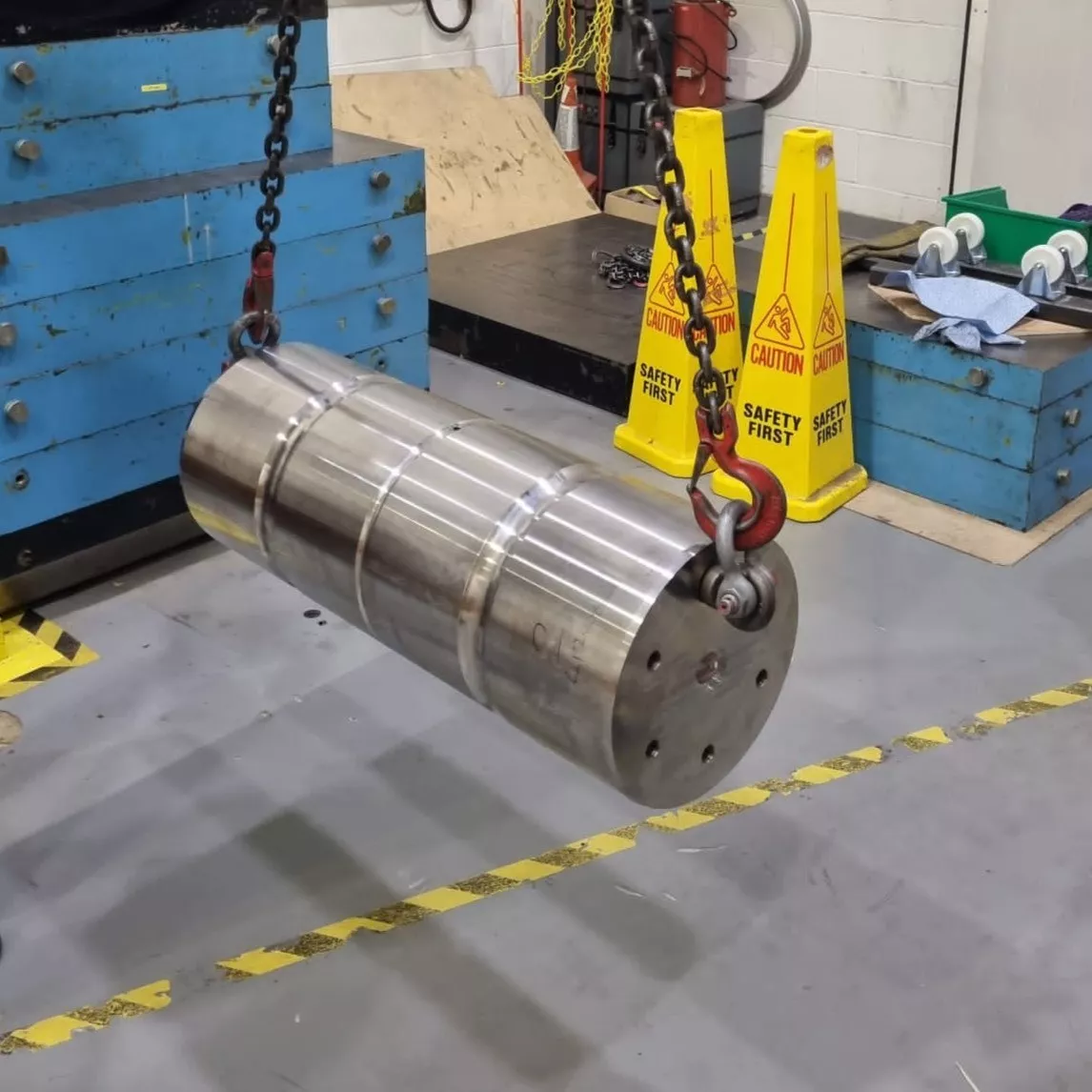
Offshore load pins: the devil is in the details
As Barge Master operates to the highest marine safety standards, the Althen load pins were also subject to stringent off-shore safety standards as set by DNV. In order to comply with this, the 1680te load pins were outfitted with completely redundant integral 4-20 mA dual measurement chains, in order to avoid any loss of signal due to component failure.
Calibration and proof load up to 150%
The pins, each weighing around 600 kg, were made out of 17-4PH stainless steel, which was heat treated twice at 1.150 °C. Additionally, the material was subjected to Charpy Impact Testing to verify its ability to absorb impacts, and was supplied with a full 3.2 Material Certificate certified by DNV. At the end of the production process, both Althen Sensors & Controls and Barge Master were present as the National Physical Laboratory in London calibrated the load pins and proof loaded each of them.
Custom Althen ALP load pin
Calibrated and proof loaded by The National Physical Laboratory in London
-
rated for1680
tonnes
-
calibrated and proof loaded up to2520
tonnes
-
or150 %
of the full range

Compensating roll, pitch and heave
The BM-Heavy Feeder compensates at the base of the tower sections for roll and pitch motions. An additional heave (up/down) compensation solution in the hook of the crane assists in eliminating the vertical motion induced by waves. The Heavy Feeder platform can operate in waves of over 2 meters high, and has a payload capacity of 700-1.500 tonnes. The installation will provide an increased workability of 40-60% more uptime during the installation of the turbines.
About Barge Master
Barge Master was founded on the determination to conquer weather downtime. Their motion compensation systems are dedicated to increasing workability at sea with innovative and practical solutions. They see motion compensation as the perfect technology to keep the load still, the equipment stable and the people safe. Their systems eliminate the need for bigger ships and provide a cost-effective solution for offshore operations. With motion compensation, working at sea becomes almost as easy as working on land. The innovative nature of the Barge Master concept is recognized by the European patent office, industry specialists and the Dutch Government through its innovations-office and several innovation awards. At Althen, we are immensely grateful and proud for the trust, cooperation, and input we experience from Barge Master and staff.
We are experts in custom heavy duty load pins and load cells, which can be tailor-made to fit existing constructions. Althen load cells are used in offshore, medical, civil engineering, and other industries where high reliability and accuracy are key requirements.