Reliable sensor technology for harsh environments in oil and gas operations
The oil and gas industry places exceptionally high demands on sensor systems. Sensors must perform reliably under extreme conditions—ranging from high pressures and temperature fluctuations to exposure to corrosive media and explosive atmospheres. In this context, robustness, precision, and long-term stability are critical.
To operate safely in hazardous areas, sensors require ATEX or IECEx certification. They must also maintain accuracy and functionality over extended periods, even when exposed to heat, humidity, and chemical stress.
For efficient, centralized process control, seamless integration into SCADA and DCS environments is essential. That’s why modern sensor solutions are equipped with remote transmission capabilities and support intelligent communication protocols, ensuring real-time monitoring of critical parameters across complex industrial systems.
Commonly used sensors in this sector
- Intrinsically safe pressure sensors To monitor pressure in boreholes and pipelines and to monitor tank levels.
- Temperature sensors Sensors accurately measure tank contents of oil, gas and condensates, and continuously monitor process and storage temperatures.
- Flowmeters Sensors record the flow of oil, gas, water and chemicals.
- Pressure sensor modules Accurate level monitoring of oil, gas and condensates.
- Vibration sensors Condition monitoring of pumps, compressors and turbines for predictive maintenance.
- Tilt- and inclinometers For monitoring pipe deformations, platform stability.
- Temperature and humidity sensors Accurate humidity monitoring of gas and air in industrial processes.
High risk factors in the oil and gas industry
In the oil and gas industry, sparks and fire are one of the biggest sources of danger for explosions. Especially for this industry, we offer an ATEX-certified sensor series that is particularly suitable for use in explosive environments. For use in "Zone 1" of refineries, we supply position sensors that monitor the position of the gas valve. These sensors can measure very small distances of only a few millimeters. We also offer the ATEX barrier to protect the sensor from combustion energy.
Industry-specific applications
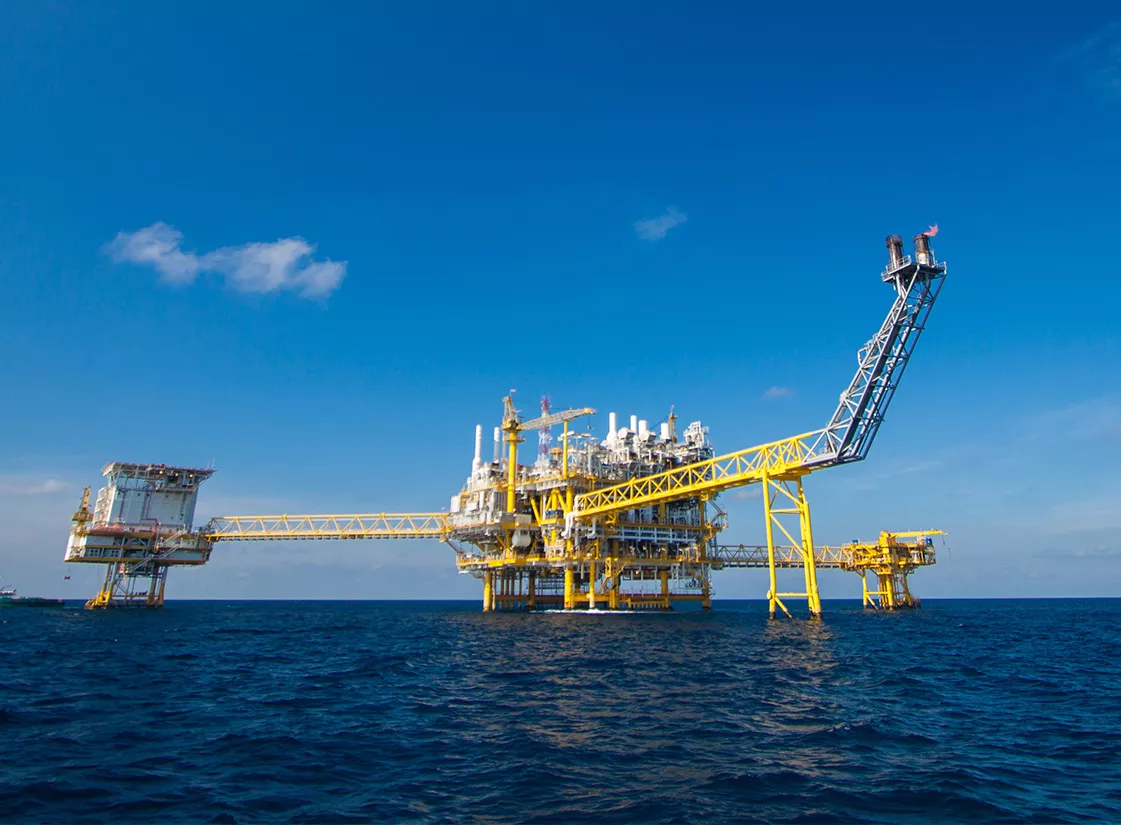
Oil, gas and mining production facilities
During the extraction stage, raw materials such as crude oil, natural gas, and coal are brought to the surface from deep underground, often under extreme pressure, high temperatures, and in corrosive environments. In such conditions, reliable sensor technology is essential to ensure safe, efficient, and uninterrupted operations.
Pressure sensors monitor borehole and production pressures, while temperature sensors are deployed in wellheads and used to track fluid temperatures throughout the system. Vibration sensors help detect early-stage anomalies in pumps and drilling equipment, enabling predictive maintenance. In addition, gas sensors detect hazardous gases such as methane or hydrogen sulfide (H₂S), which pose both explosive and toxic risks.
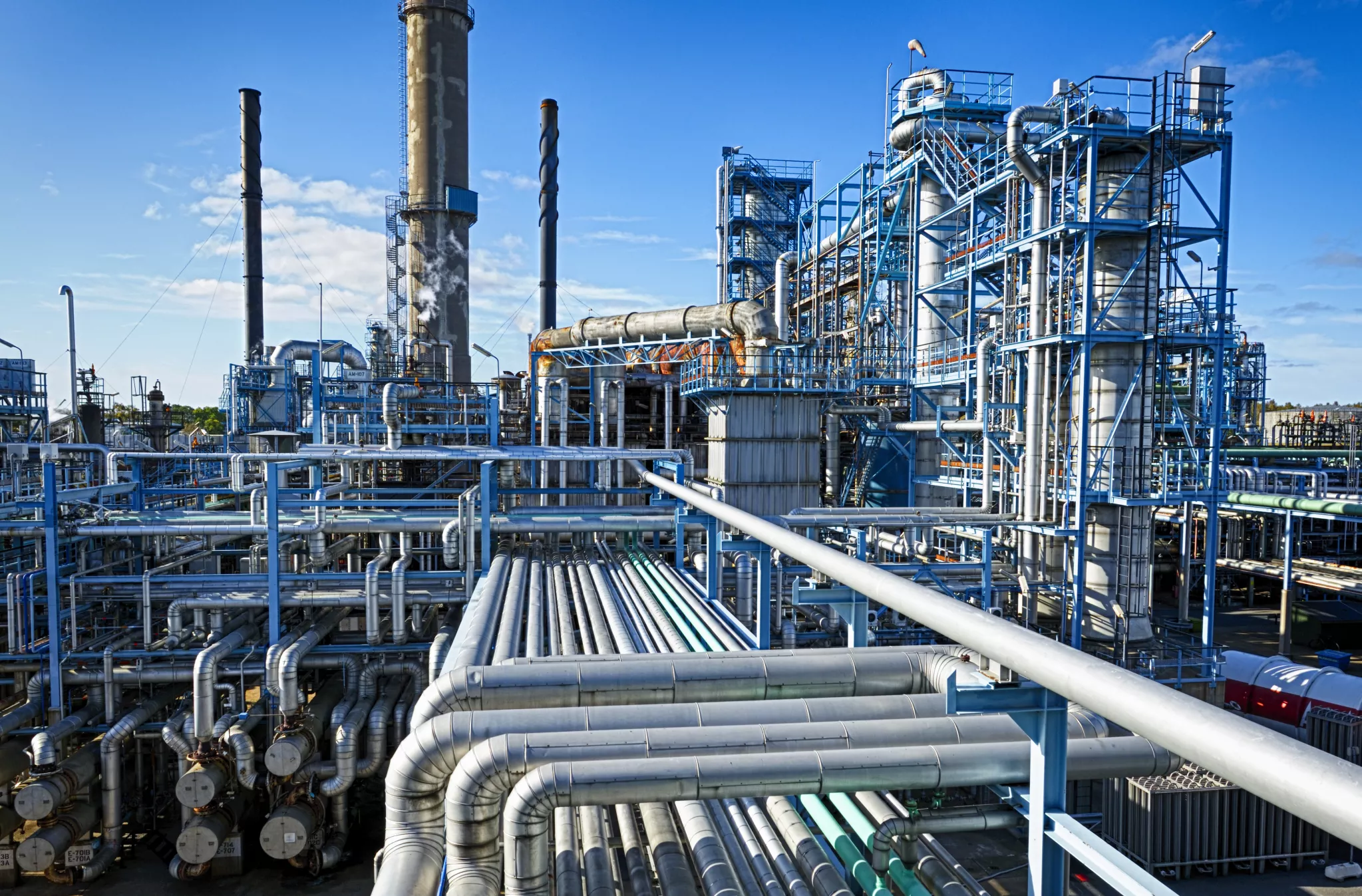
Safe and reliable pipeline transportation
Continuous monitoring is essential for safe transport of oil, gas and other process media, especially across long distances and under fluctuating environmental conditions. Sensors play a critical role in maintaining system integrity and operational safety.
Pressure sensors and flowmeters enable early leak detection and accurate pressure monitoring. Temperature sensors help prevent condensation, icing, and overheating. Meanwhile, inclination sensors detect soil movement or subsidence at an early stage, reducing the risk of structural damage to underground pipelines.
By continuously monitoring these key parameters, operators can prevent incidents, reduce downtime, and ensure safe, uninterrupted operation of vital transport infrastructure.
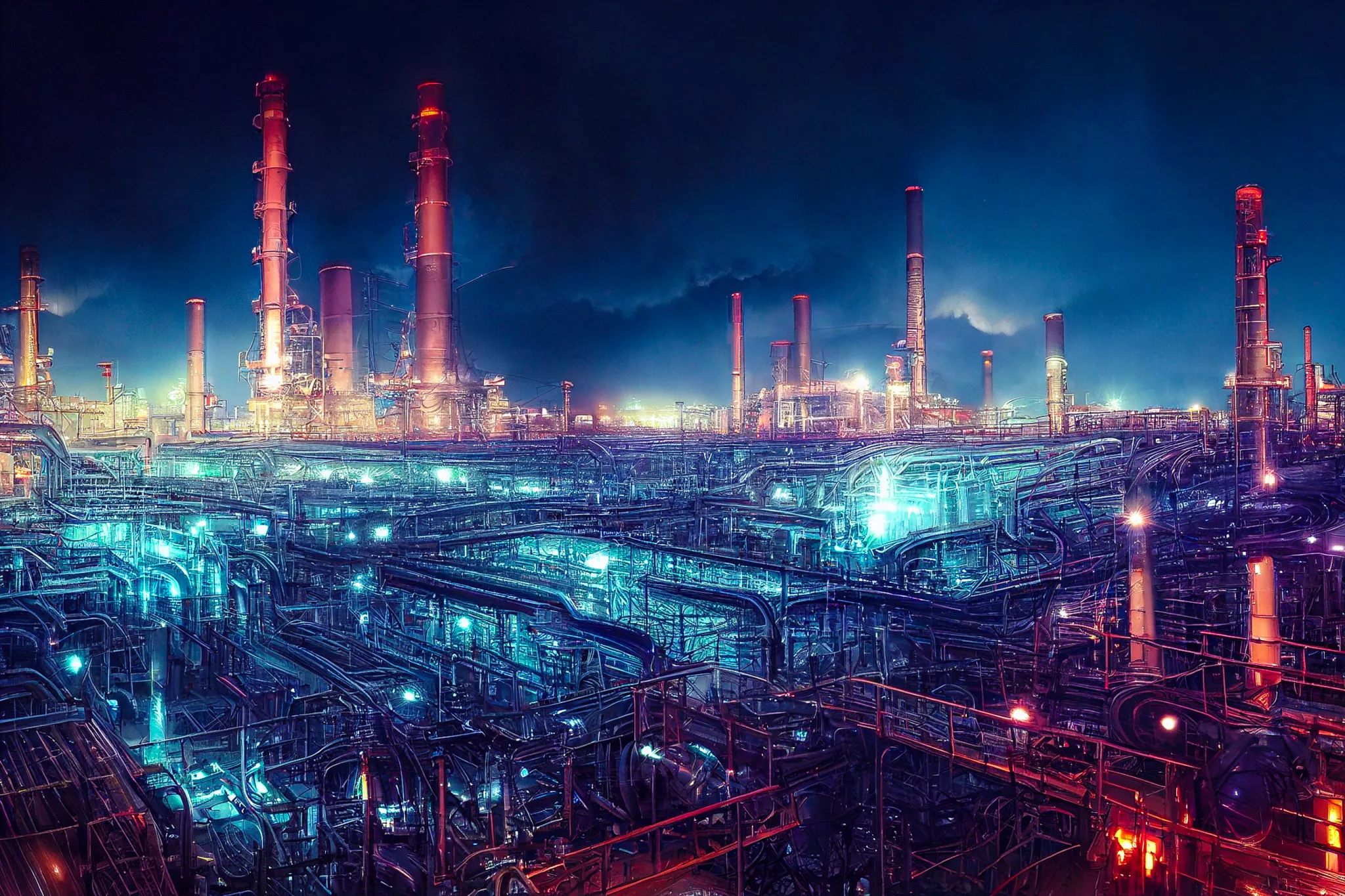
Refineries, power stations, chemical plants
Further processing of raw materials, such as cracking, desulfurization, or power generation, demands precise control over complex industrial processes. At the same time, facilities must comply with the strictest safety standards, particularly in potentially explosive environments.
These operations rely on submersible pressure level sensors to monitor storage tanks and reactors, as well as pressure and temperature sensors for accurate control within pipelines and reaction vessels. Gas detectors provide early warning of flammable or toxic gases, helping to prevent hazardous situations before they escalate.
Together, these sensors form a critical foundation for safe, reliable, and efficient process operations in the chemical and petrochemical industries.
-
A-Class QualityIn product an process
-
Long-term PartnershipWith all stakeholders
-
Reliable and ExperiencedProven trackrecord over 75 years
-
Innovative and NewState-of-the-art products and developments
Product categories
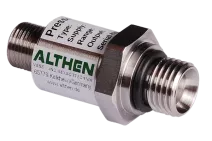
General purpose pressure sensors
- Measuring range -1 to 10.000 bar
- Standard Low-cost
- Variety of options available
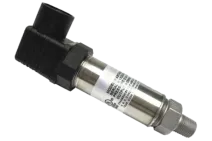
Intrinsically safe pressure sensors
- Measuring range 0 to 1.600 bar
- ATEX approved for hazardous areas
- Durable, stable, reliable & accurate
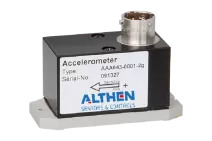
Servo accelerometers
- Measuring range ±0.1 g to ±20 g
- Resolution as great as 0.0005 % FRO
- Good shock resistance and stability
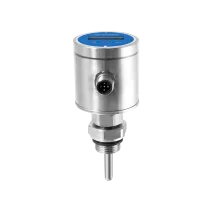
Flow switches
- Self-luminous OLED display
- Optional power supply & mounting interfaces
- Overvoltage, overcurrent, reverse polarity protection
- With temperature compensation and calibration
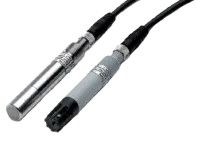
Temperature, humidity & other sensors
- Special for temperature and humidity
- For all data loggers
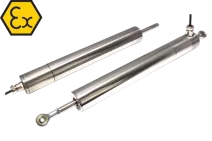
Intrinsically safe position sensors
- Measurement range 0 to 800 mm
- For hazardous / explosive environments
- Inductive measuring to prevent wear
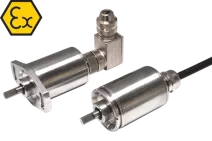
Intrinsically safe inductive rotary sensors
- Measuring range 5º to 160º
- Approved for use in harsh environments
- Excellent linearity down to ≤ ±0.1%
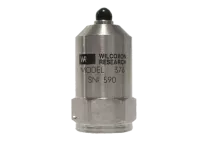
High-temperature vibration sensors
- Measuring range 10 g to 4.000 g
- For application in temperatures over 120°C
- Excellent sensitivity & low noise
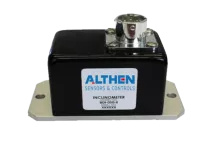
Geotechnical (electrolytic) inclinometers
- Measuring range ±0.00000575° to ±90°
- Resolution as low as <2.5 nanoradians
- For monitoring infrastructures
Our clients
Mining
Working conditions in the mining industry are demanding and potentially hazardous. Timely detection of wear or malfunctioning equipment is essential—not only for worker safety but also for the efficiency of daily operations. Mining machinery often runs around the clock and is continuously exposed to dust, moisture, and high temperatures.
Our mining customers rely on ATEX-certified vibration sensors and acceleration sensors for condition monitoring and predictive maintenance. These robust sensors feature stainless steel housings designed to withstand the harshest environments. Installed on rotating components such as motors, bearings, and pumps, they enable continuous performance monitoring, reduce unplanned downtime, and contribute to a safer working environment.
Our projects
Related products
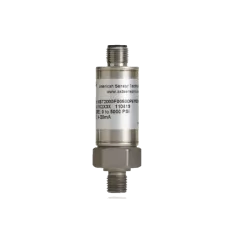
AST2000 Hydrogen Pressure Transducer
- Measuring range: 0 - 2 to 0 - 700 bar
- For hydrogen pressure sensing applications
- With high performance digital compensation
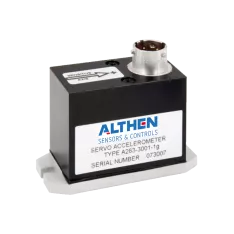
AAA260 Servo Accelerometer
- High resolution down to 0.05 mg
- Closed loop force balance system
- Flight qualified versions available
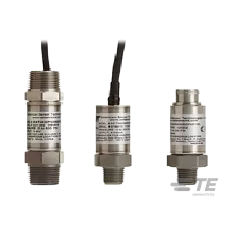
AST4400 Intrinsically Safe Pressure Transducer
- Measuring range: 0 - 2 to 0 - 1.350 bar
- No Oil, Welds or Internal O-rings
- -40 to +80°C Operating temperature
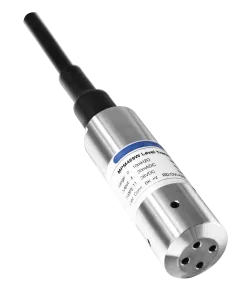
MPM489W Submersible level transmitter
- Integrated structure, no extra adjustment required
- Intrinsic safety type, Ex ia IIC T6 Ga
- Explosion-proof type, Ex d IIC T6 Gb
- CE, RoHS and CCS approved
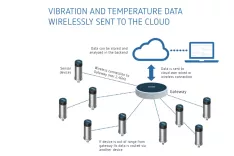
Wireless IoT Vibration Measurement Solution
- Scalable and reliable
- Data dashboard service available
- Reduces maintenance costs and machinery downtime
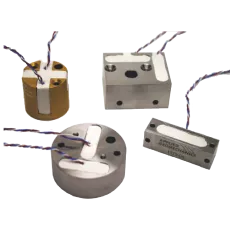
755-High-Gain and 756-Mid-Range Miniature Tilt Sensors
- for special vacuum applications
- for precise measurement and control applications
- applicable when space is limited
The benefits of sensor technology in the oil, gas and coal industry
- Increased operational safety
Sensors continuously monitor critical systems such as pressure lines, storage tanks, feed pumps, and gas installations. They instantly detect hazardous conditions like overpressure, gas leaks, or overheating. This enables immediate intervention, minimizing risks to both personnel and the environment, and ensuring safer, more reliable operations. - Early fault detection
Pressure, vibration, and temperature sensors identify abnormal system behavior at an early stage, such as leaks, irregular pump operation, or the onset of material fatigue. This early detection enables timely intervention, helping to prevent equipment failure, reduce damage, and maintain reliable system performance. - Minimize downtime
Thanks to predictive maintenance based on sensor readings, repairs can be scheduled before a shutdown occurs. This increases system availability, reduces costly emergency calls and saves production downtime. - Explosion-proof and compliant
In hazardous areas (ATEX zones), specially certified sensors ensure safe and compliant operation and monitoring. Refineries, gas compressor stations and offshore platforms place high demands on explosion safety. Deployment of certified sensors is not only very important, but often required by applicable regulations. - Efficient maintenance and reduced operating costs
Sensor-based monitoring minimizes unnecessary maintenance, extends service intervals, and enables the targeted use of personnel and resources. At the same time, it boosts operational efficiency by optimizing processes and detecting early-stage faults, long before they result in equipment failure or costly downtime.